Abstract
Fe-TiC composite coatings were produced on the surface of plain carbon steel by submerged arc cladding process. Mixtures of cast iron chips and ferrotitanium powder with different weight ratio between 1 and 6 were used as the alloying element sources. Cladding was performed by carbon‑manganese steel wire. Results showed that increase in the cast iron to ferrotitanium (CTF) weight ratio from 1 to 6 decreased the Ti wt% from 3.93 to 0.96 and increased the carbon concentration from 0.26 to 0.51 wt%. Titanium carbide reinforcing particles were detected in the microstructures of all coatings. Meanwhile, their size and volume fraction, as well as the microstructure of the matrix strongly was depending on the CTF weight ratio. The highest mean hardness value of 960 HV was obtained for the cladding produced by the CTF weight ratio of 6 with the TiC reinforced martensitic microstructure. Pin on disk wear test results showed that the hardest coating had the best wear resistance with the plowing and cutting wear mechanisms.
Introduction
Surface engineering and coating processes deal with the improvement in the surface properties of the materials without altering the bulk material properties. Surface modification and surface coatings are two main categories of the surface engineering methods. Surface modification routes including; carburizing, flame hardening, etc. usually improve the surface properties of the bulk material. In contrast, surface coating processes involve depositing a layer with various thicknesses onto the substrate [1]. Thick coating layers usually are deposited by cladding processes to make better the corrosion and wear resistances of the substrate [1,2]. Welding processes like gas tungsten arc welding (GTAW) [3,4], gas metal arc welding (GMAW) [5], submerged arc welding (SAW) [6], shielded metal arc welding(SMAW) [7] and laser welding [8] usually are used for cladding. Despite the similarities of these processes, the main advantage of the submerged arc cladding method is the ability to produce very thick overlays in a single track [[9], [10], [11], [12], [13]]. The principles of this process are explained in the literature, extensively [11,14].
Up to now, various ceramic particle reinforced iron based composites have been applied on the surface of steel substrates to improve their wear resistance [[15], [16], [17], [18]]. In this regard, titanium carbide (TiC) [15,17,18], tungsten carbide (WC) [19,20] and chromium carbide (Cr7C3) [21,22] particles were used as the reinforcing phases. Among them, TiC with high hardness and melting point and compatibility with the Fe matrix is a good candidate as the reinforcement [17,23]. During cladding, the reinforcing particles may be added to the melt pool externally (ex-situ methods), or they may form into the melt during solidification (In-situ methods). It is generally accepted that the in-situ particles are more stable than the ex-situ particles, thermodynamically and have a tight and clean interface with the matrix [24].
Heretofore, there are some investigations on the development of hard coatings by submerged arc (SA) cladding process [9,10]. For example, Lu et al. [10] investigated the effect of process parameters on the microstructure, hardness and wear properties of the Fe–Mn–Cr–Mo–V alloy coatings produced by submerged arc welding process. Their results showed that the formation of martensitic microstructure improved hardness of the coating to 604 HV. Moreover, the wear properties of the claddings were not affected considerably by process parameters. In another experiment, Zahiri et al. [9] studied the microstructure and wear resistance of the Fe–Cr–C hardfacing alloy produced by submerged arc cladding process on the surface of mild steel substrate. Mixtures of ferrochrome, cast iron chips and stainless steel shots were used as alloying element sources. Moreover, in some samples the cast iron chips was replaced with boron-rich powders. Their results showed that hypoeutectic, eutectic and hypereutectic Fe-Cr-C alloys were produced by altering the composition of the mixture. In addition, carbide and boride phases were observed in the microstructures. These micro constituents increased hardness of the coatings to 66 HRC and improved its wear resistance, considerably.
Although, there are many published researches on the fabrication of in-situ Fe-TiC composite coatings on the surface of steel by GTAW, plasma arc welding and laser cladding processes, but, the coating’s thickness produced by these methods is limited. Moreover, the low heat input of the mentioned processes diminishes the dilution between the coating and substrate which can alter the properties of the coatings. However, the SA cladding process is used for fabrication of thick coatings in a single track. The large heat input of this process may result to microstructural changes and the formation of coatings which have completely different characteristics from those produced by GTAW, Laser and plasma processes. Therefore, finding a deep understanding about the formation of thick coatings produced by the SA cladding method and their properties is necessary from both scientific and technical points of view. To the best knowledge of authors, a systematic research relating to the fabrication of Fe–TiC composite coatings on the surface of steel by submerged arc cladding process is scarce. Therefore, the present study was conducted to produce thick Fe-TiC composite coatings on the surface of mild carbon steel using ferrotitanium and cast iron precursor mixtures. Then, the effects of precursor composition on the microstructure, hardness and wear properties of the coatings were explored.
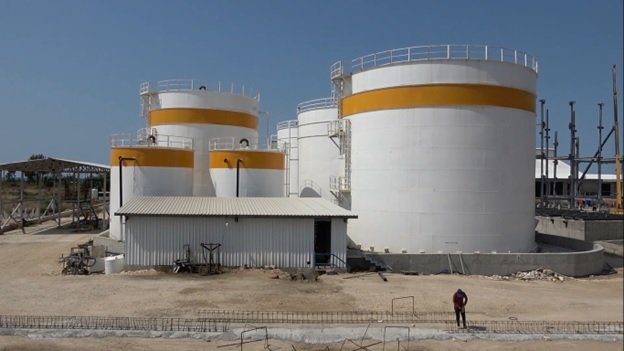
Section snippets
Materials and methods
Low carbon steel plates with the dimensions of 10 × 100 × 200 mm3 were used as the substrate. Table 1 lists the chemical compositions of the starting materials.
In order to have almost the same amounts of reactive mixture per unit length of the weld for all coatings, a single bevel groove was prepared along the length of each plate with the depth of 6 mm and bevel angle of 60°. After that, two plates were adjusted in such a way that a partial penetration single V groove was formed.
Gray cast iron
Claddings appearance and chemical composition
Fig. 1(a) to (d) shows the appearance of various coatings produced by different CTF ratios.
At low CTF, the coating had an irregular surface morphology as shown in Figs. 1(a) and (b). Furthermore, slag inclusion and cluster porosity were detected on the surface of the weld profiles. It is noteworthy that the combustion flame could easily be observed beneath the welding powders during cladding process at low CTF ratios. Moreover, the presence of cluster porosity showed the inadequate shielding of
Conclusion
Thick Fe-TiC composite coatings were overlaid on the surface of mild steel by submerged arc cladding process. Ferrotitanium powder and cast iron chips were used as the precursor of the Ti and C alloying elements. Then, the effects of carbon to ferrotitanium weight ratio (CTF) of the mixture on the structure, microstructure, hardness and wear properties of the coatings were investigated. The main results can be summarized as follows:
1.The chemical composition of the coatings was influenced by the
Author links open overlay panelH. Zeinali Moghaddam, M. Sharifitabar
, G. RoudiniDepartment of Materials Engineering, Faculty of Engineering, University of Sistan and Baluchestan, Zahedan, P.O. Box: 98135-674, Iran
Received 29 September 2018, Revised 23 December 2018, Accepted 15 January 2019, Available online 15 January 2019, Version of Record 16 January 2019.
نویسنده مقاله: دکتر محمود شریفی تبار/مدیرعامل وسپار